When selecting crash bars, you'll want to weigh stainless steel for its exceptional durability and corrosion resistance, especially grade 304. Aluminum, specifically 6061 alloy, offers a lightweight alternative, enhancing bike handling while maintaining strength. You might also encounter plastic-covered options, combining a steel or aluminum core with a plastic shell for additional impact absorption. Make sure you're mindful of corrosion resistance; stainless steel and titanium provide the best protection, while aluminum demands proper treatments. Each material's tensile strength directly influences its impact resistance and overall performance during crashes. Keep exploring to access the perfect balance of protection and performance.
Key Takeaways
- Stainless Steel (Grade 304): Offers exceptional durability, high tensile strength (120,000 psi), and outstanding corrosion resistance.
- 6061 Aluminum Alloy: Lightweight with 40-42,000 psi tensile strength, enhancing handling and performance while providing effective impact absorption.
- Plastic-Covered Bars: Combine steel/aluminum cores with plastic coatings for added impact absorption and aesthetic appeal, requiring regular inspections.
- 4130 Steel Alloy: High tensile strength (97,000 psi) and excellent corrosion resistance, balancing strength and weight.
- Advanced Manufacturing: Techniques like 3D printing and TIG welding ensure structural integrity and optimal performance in crash bar production.
Stainless Steel Crash Bars
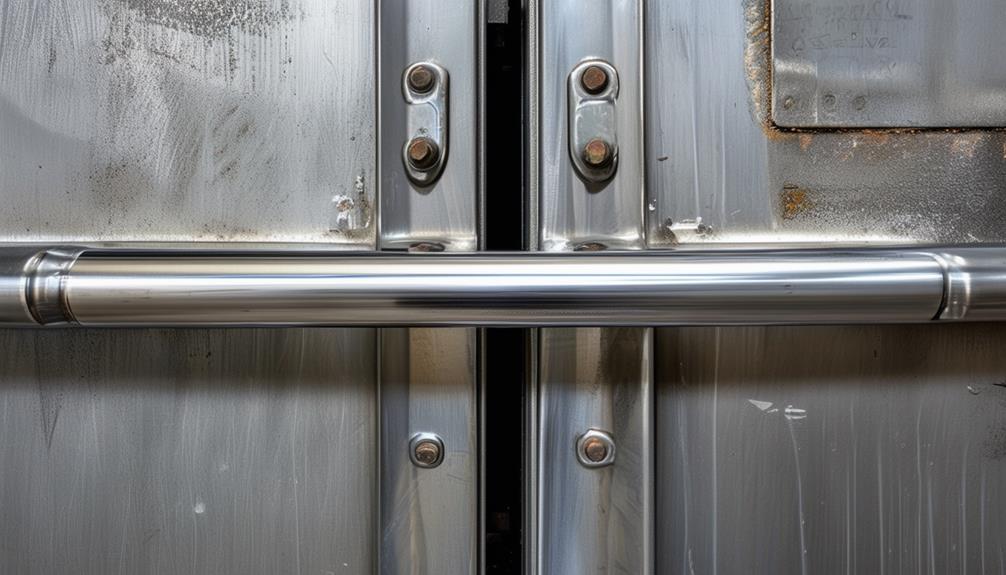
When it comes to choosing crash bars for your motorcycle, stainless steel options, particularly those made from grade 304, stand out for their exceptional durability. With a tensile strength of approximately 120,000 psi, these stainless steel crash bars offer impressive resistance to deformation under stress. This high level of crash bar durability guarantees that your motorcycle will be well-protected in various impact scenarios. Stainless steel crash bars also excel in corrosion resistance, making them ideal for diverse environmental conditions. This means they won't easily succumb to rust or wear, thereby prolonging their lifespan compared to other materials. Additionally, their design mechanisms often incorporate advanced features for enhanced protection, as discussed in global usage trends.
However, fabricating stainless steel requires specific techniques. TIG welding is essential to maintain the structural integrity and prevent distortion, especially in thinner designs. While stainless steel is heavier than aluminum, its strength-to-weight ratio provides a balanced solution that enhances protection without greatly compromising handling. Proper design and fabrication are vital to avoid stress transfer to the motorcycle's frame or engine, which could cause damage during impacts. Consequently, when considering the overall protective capabilities and longevity, stainless steel crash bars offer a robust and reliable option for motorcycle crash protection.
Aluminum Crash Bars
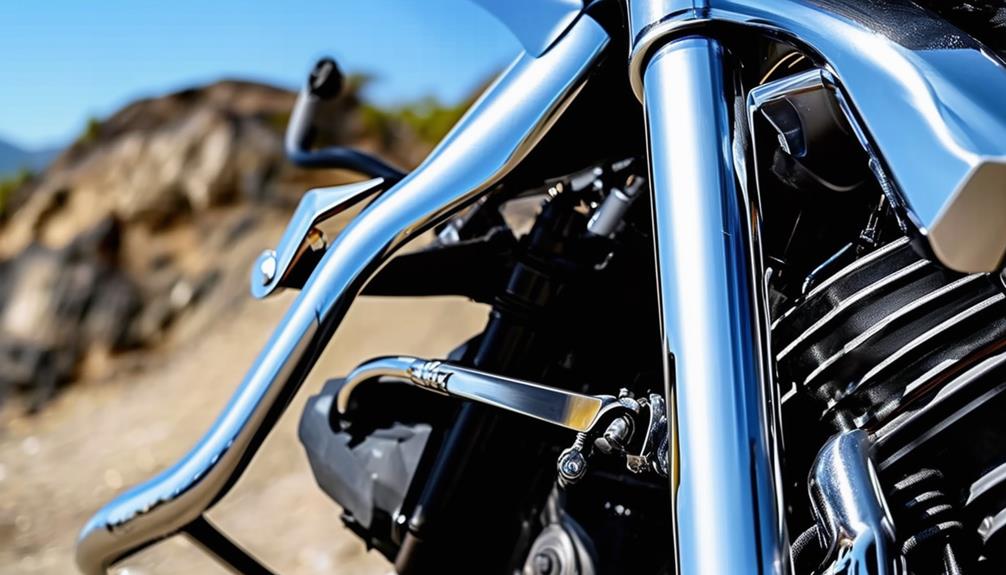
While stainless steel crash bars boast impressive durability and corrosion resistance, aluminum crash bars bring unique advantages to the table. Leveraging their lightweight properties, aluminum crash bars enhance motorcycle handling and performance, essential elements when considering crash bar material comparison. Typically crafted from 6061 aluminum alloy, these bars provide a tensile strength of approximately 40-42,000 psi, striking an ideal balance between strength and weight. As highlighted in the crash bars vs. push bars comparison, both materials have their unique perks and applications.
In crash bar durability testing, aluminum bars demonstrate their ability to effectively absorb impact and distribute energy during a crash. This minimizes damage to your motorcycle and offers considerable rider protection. Despite their lightweight nature, aluminum crash bars are engineered to match or even surpass the strength of steel bars. By optimizing wall thickness and structural integrity, you'll find that aluminum can handle notable impacts without compromising safety.
Another key advantage is aluminum's high resistance to corrosion. This makes aluminum crash bars suitable for various riding conditions, markedly reducing maintenance needs compared to other materials. When you weigh the benefits in a crash bar material comparison, aluminum crash bars clearly offer a compelling option, combining strength, lightweight performance, and minimal upkeep.
PlasticCovered Crash Bars
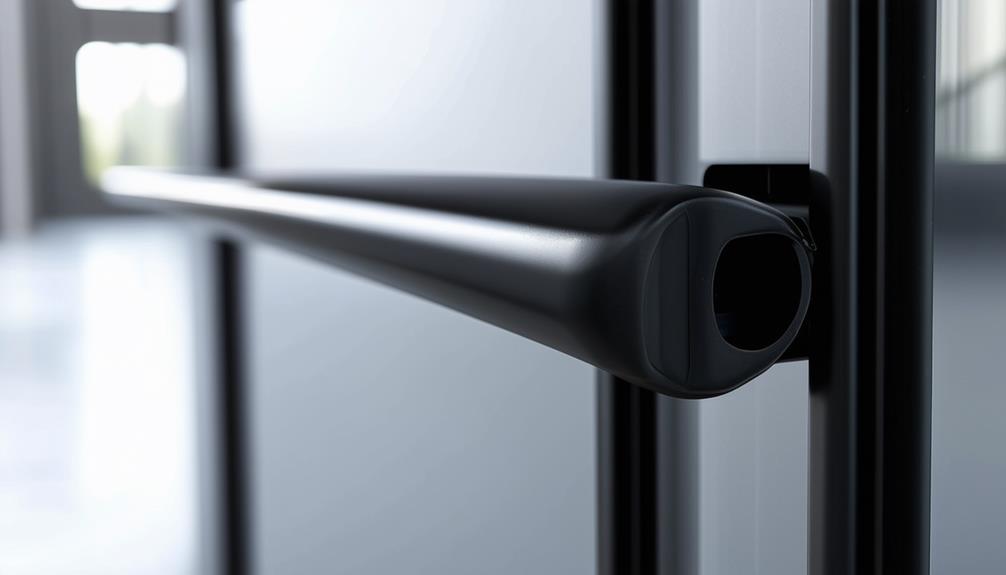
You might be intrigued by plastic-covered crash bars, which combine the robustness of steel or aluminum cores with the added benefits of a plastic coating. These bars provide not only the strength necessary to protect your motorcycle but also help absorb impacts, reducing crash bar wear and tear. The plastic layer acts as a shield against scratches and minor dings, preserving the bar's integrity over time. For those interested in emergency egress solutions, panic bars also offer an excellent blend of safety and functionality, especially in commercial settings.
One of the appealing aspects of plastic-covered crash bars is their ability to enhance your bike's aesthetic appeal. The plastic coating can be customized to match or complement your motorcycle, providing a sleek and polished look. However, it's important to note that extreme heat can cause the plastic to deform, potentially compromising its protective qualities.
- Noise and Vibration Reduction: The plastic layer helps dampen noise and vibrations, contributing to a more comfortable ride.
- Environmental Protection: The coating offers additional defense against environmental factors like rain and debris, though periodic maintenance is important.
- Inspection Needs: Regular checks are vital as the plastic can wear down, exposing the metal core and necessitating repairs or replacements.
Understanding these factors will help you make an informed decision about incorporating plastic-covered crash bars into your motorcycle's setup.
Corrosion Resistance
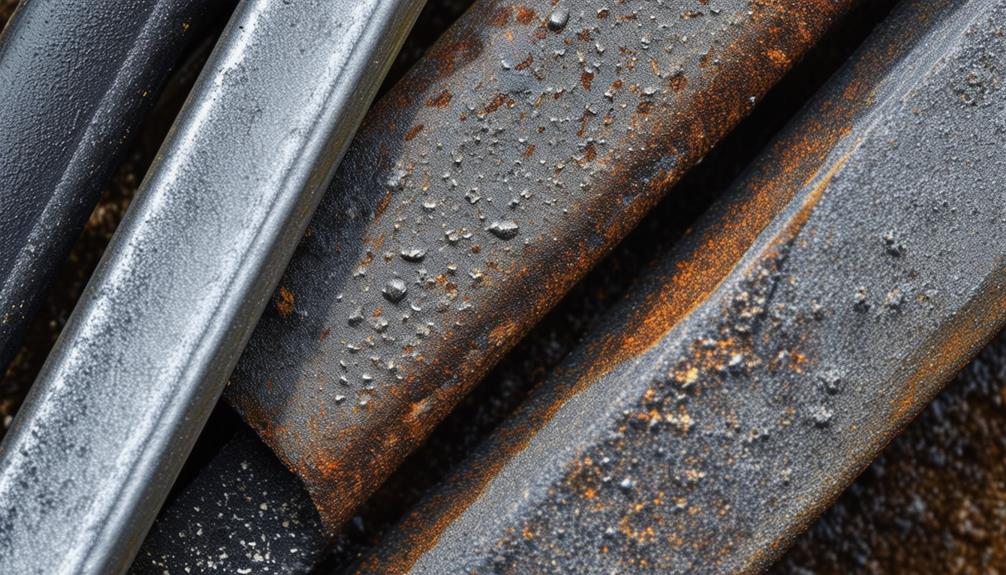
Given the vital role crash bars play in protecting your motorcycle, their resistance to corrosion can't be overlooked. When evaluating crash bar corrosion resistance, it's important to take into account crash bar material specifications. Stainless steel, particularly grades 304 and 316, stands out for its excellent resistance to corrosion. The high chromium content in these grades forms a passive layer that shields against moisture and harsh environments, making them ideal for long-term durability. These same material specifications are often regarded in the manufacturing of electronic panic bars due to their need for reliability in emergency situations.
Aluminum crash bars, known for their lightweight properties, also offer good resistance to rust and oxidation. However, they require proper treatment or coating to prevent long-term degradation. Anodizing is a common surface treatment that greatly enhances aluminum's corrosion resistance.
On the other hand, carbon steel is more susceptible to rust and corrosion without protective coatings. Regular maintenance and surface treatments like galvanization are vital to maintain its integrity in exposed conditions.
Titanium offers superior corrosion resistance compared to both aluminum and steel. Its natural ability to form a stable oxide layer is key, making it an excellent choice for enduring harsh environments without considerable wear.
Impact Resistance
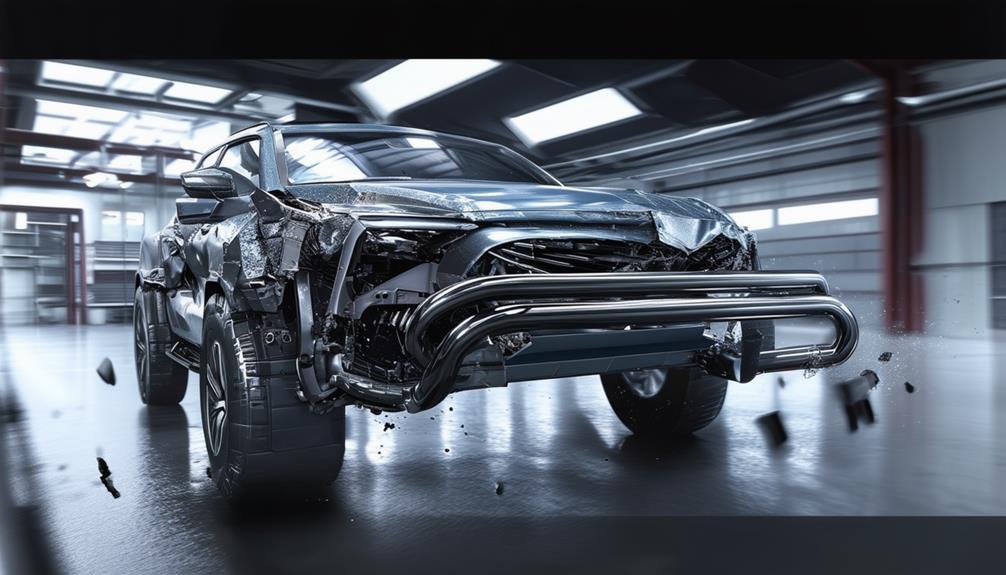
Understanding the corrosion resistance of crash bars is fundamental, but their ability to withstand impact is equally vital. When selecting durable crash bars, you need to take into account the material's tensile strength and its ability to absorb and distribute impact energy. Crash bar strength is greatly influenced by the material used. For instance, 4130 steel, with its 97,000 psi tensile strength, provides robust impact resistance, guaranteeing your motorcycle remains protected during a collision. Case studies have demonstrated the effectiveness of using high tensile strength materials in real-world scenarios.
Aluminum crash bars, when engineered correctly, can rival steel in strength, offering a beneficial strength-to-weight ratio. This not only enhances bike handling but also assures you don't compromise on protection. Stainless steel, particularly grade 304, boasts a tensile strength of around 120,000 psi, making it exceptionally effective at absorbing impact energy and protecting your bike.
Materials with high ductility, like carbon steel, might bend rather than crack under stress. This characteristic can prevent further damage to your motorcycle's frame and components. Additionally, the design and construction of crash bars are essential. Poor alignment or weak mounting can result in inadequate protection during a crash.
- 4130 steel: 97,000 psi tensile strength
- Aluminum: High strength-to-weight ratio
- 304 stainless steel: 120,000 psi tensile strength
Environmental Durability
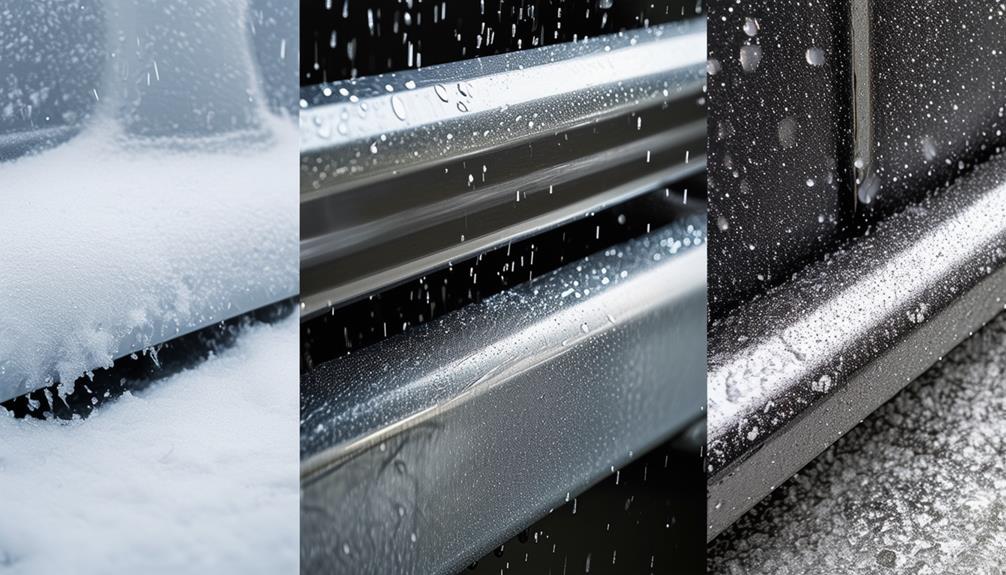
When evaluating the environmental durability of crash bars, material choice plays a significant role. You'll find that stainless steel is an excellent option due to its superior corrosion resistance. Unlike carbon steel, which can rust when exposed to moisture without protective coatings, stainless steel maintains its integrity, guaranteeing crash bar safety and longevity.
Aluminum crash bars, while lightweight, present another option. However, they're prone to oxidation in harsh environments. Regular inspections and treatments are necessary to maintain their structural integrity. This upkeep is vital if you're looking to guarantee long-term crash bar material safety. For instance, retrofit options can help in updating existing installations to meet current standards and enhance durability.
For a balanced approach, consider 4130 steel. Its tensile strength provides both durability and corrosion resistance, making it suitable for a variety of environmental conditions. High-quality finishes, such as powder coating or anodizing, can further enhance the environmental durability of crash bars. These finishes act as protective layers against scratches, moisture, and UV exposure, prolonging crash bar longevity.
In extreme conditions like high humidity or salt exposure, selecting materials that can withstand such environments without compromising structural integrity is essential. By prioritizing materials with proven durability, you guarantee the longevity and safety of your crash bars.
VandalResistant Crash Bars
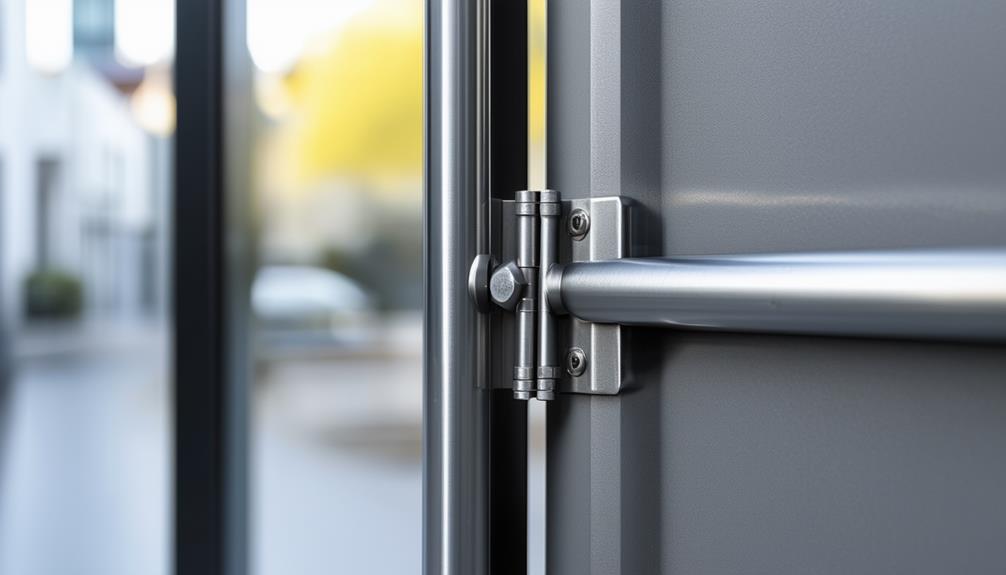
While environmental durability is paramount, the need for vandal-resistant crash bars can't be understated. When you're selecting crash bar materials, opting for high-strength options like stainless steel or 4130 steel is essential. These heavy-duty crash bars enhance durability and provide superior resistance to both impact and abrasion, safeguarding your motorcycle from potential vandalism. Remarkably, manufacturers like Von Duprin excel in producing high-quality security hardware, which can be a useful reference for understanding the standards of durability and resistance required.
To further extend their lifespan, these bars often feature protective coatings or finishes that prevent corrosion and wear, even in harsh environments. Additionally, the design includes reinforced mounting points, guaranteeing they can withstand heavy impacts without compromising the structural integrity of your motorcycle.
Consider these benefits of vandal-resistant crash bars:
- High-Strength Materials: Stainless steel and 4130 steel offer enhanced durability and resistance to impact and abrasion.
- Protective Coatings: Special finishes prevent corrosion and wear, greatly extending the lifespan of the crash bars.
- Reinforced Mounting Points: Guarantees the bars can withstand heavy impacts, deterring vandalism without compromising structural integrity.
Proper installation is vital. Misalignment can lead to structural weaknesses, reducing the effectiveness of these heavy-duty crash bars. By paying attention to these details, you confirm your motorcycle remains protected from both vandalism and accidents.
Testing Crash Bar Durability
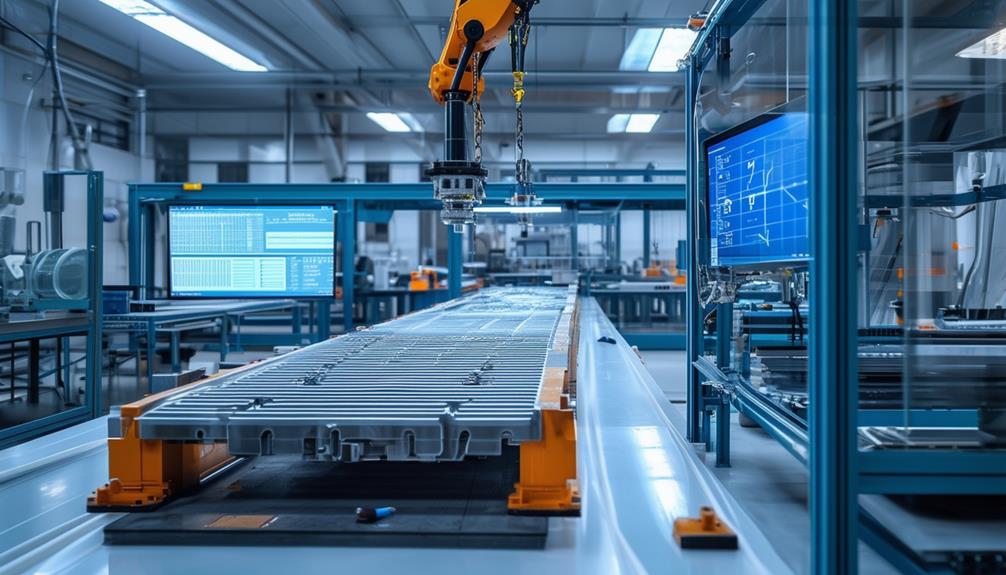
Evaluating crash bar durability involves rigorous testing methods to guarantee their effectiveness and longevity. Significant tests include impact testing, where crash bars are subjected to controlled collisions. This measures their ability to absorb and distribute impact energy without structural failure. Materials like 4130 steel and stainless steel are often highlighted in any crash bar material guide due to their high tensile strength. For instance, 4130 steel boasts a tensile strength of approximately 97,000 psi, making it a robust choice in crash bar material selection. Before installing, it's essential to take into account the pre-installation checklist specific to your door type to avoid errors.
Fatigue resistance testing is another important method. Here, crash bars undergo repeated stress cycles to simulate real-world use. This process helps assess the lifespan of the bars and their potential for failure over time. Additionally, environmental testing evaluates how crash bars hold up under corrosive elements and extreme temperatures, ensuring they maintain integrity and performance in diverse riding conditions.
Lastly, real-world feedback from riders who have tested crash bars in various terrains and accident scenarios adds invaluable data. This feedback complements laboratory results, providing a thorough understanding of crash bar durability and effectiveness in protecting both the motorcycle and its rider.
Comparison of Materials
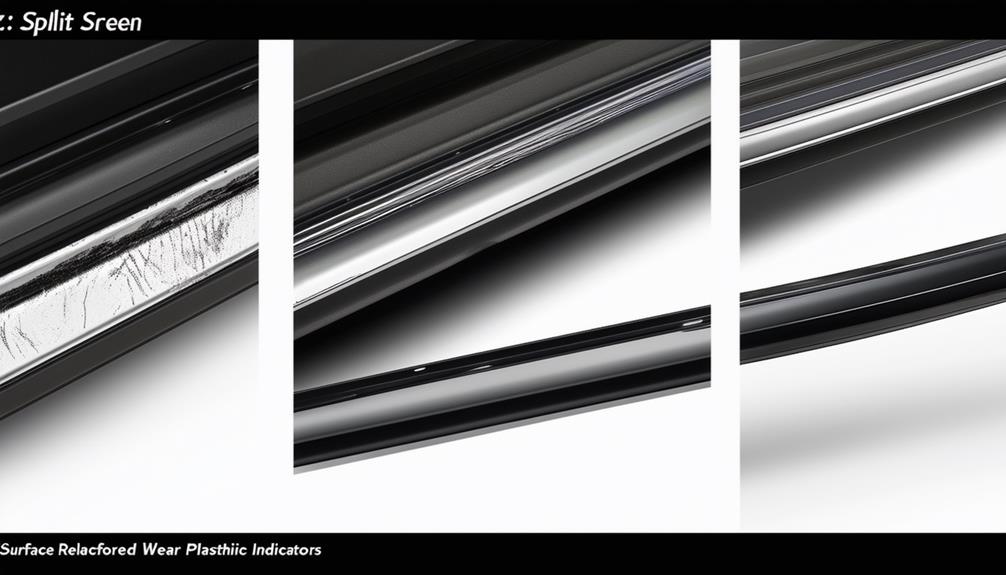
Understanding the rigorous testing methods is fundamental, but so is knowing the materials that make up these vital components. When comparing crash bar materials, you need to evaluate the pros and cons of each option. Low Rate Locksmith also offers reliable and compliant solutions for panic bars, which are essential for business safety.
Aluminum crash bars weigh around 6.1 lbs, making them lightweight and excellent for improving bike handling. However, they require proper engineering to match the strength of steel.
Stainless steel, particularly grade 304, offers high tensile strength of approximately 120,000 psi and exceptional durability. It's a popular choice for crash bars designed to withstand harsh conditions.
Carbon steel is generally less expensive and easier to work with. While it's heavier and may not provide the same level of protection as stainless steel or aluminum, it remains a viable option due to its cost-effectiveness.
4130 steel provides a balance between weight and strength with a tensile strength of about 97,000 psi, making it suitable for extreme conditions.
Titanium is lightweight and highly corrosion-resistant but requires specialized welding techniques due to its reactivity, making it less common compared to other crash bar metals.
- Aluminum: Lightweight, excellent handling, engineering required for strength.
- Stainless Steel: High tensile strength, excellent durability.
- Carbon Steel: Cost-effective, heavier, easier to work with.
Innovations in Crash Bar Materials
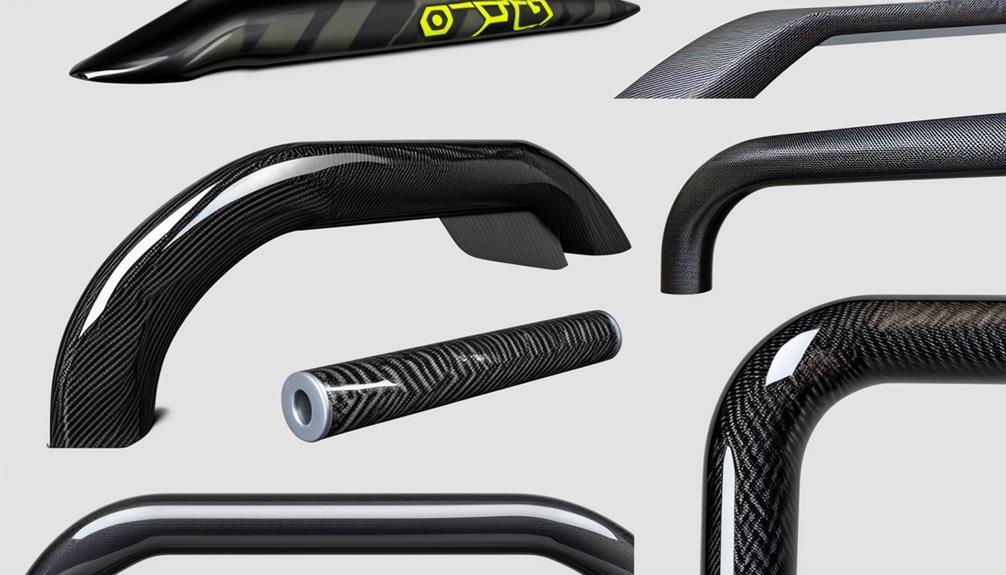
Innovations in crash bar materials are revolutionizing safety and performance in unprecedented ways. The best materials for crash bars now include high-tensile steel alloys, advanced aluminum alloys, titanium, and even composite materials. Each of these innovations offers distinct advantages regarding strength, weight, and durability.
High-tensile steel alloys, such as 4130, balance strength and weight with a tensile strength of about 97,000 psi. This makes them highly effective in protecting your bike without adding unnecessary bulk. Advanced aluminum alloys, like 6061, are engineered to provide similar strength to steel while considerably reducing weight, enhancing bike handling.
Titanium stands out as an exceptionally lightweight and corrosion-resistant option. However, it requires specialized welding techniques due to its reactivity. Meanwhile, ongoing research into composite materials aims to combine the shock-absorbing properties of polymers with the structural integrity of metals, resulting in superior performance during crashes.
These innovations are further optimized through advanced manufacturing techniques like 3D printing, allowing for complex geometries that enhance crash bar effectiveness while minimizing weight.
Material Type | Key Advantages |
---|---|
4130 Steel Alloy | High strength, balanced weight |
6061 Aluminum Alloy | Comparable strength to steel, lighter |
Titanium | Lightweight, corrosion-resistant |
Composites | Shock-absorbing, strong structural integrity |
Durable Crash Bar Solutions: Low Rate Locksmith's Commitment to Quality Materials
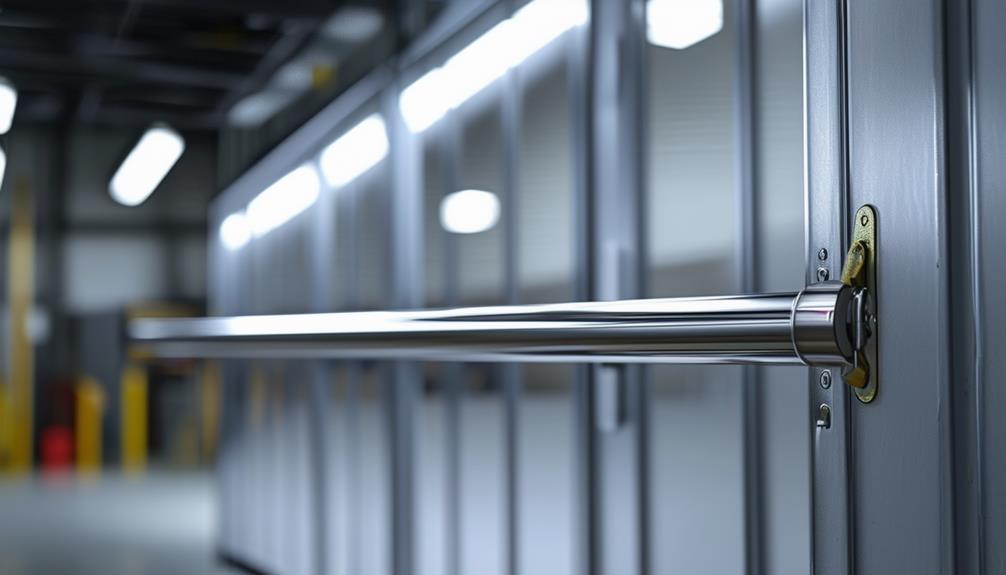
While evaluating the durability of crash bars, Low Rate Locksmith demonstrates a steadfast commitment to employing quality materials that guarantee both safety and longevity. They understand that selecting the right material can make all the difference when it comes to the performance and durability of crash bars. In addition to using high-quality materials, they offer affordable installation services to guarantee businesses can enhance their safety without breaking the bank.
Stainless steel, with its tensile strength of approximately 120,000 psi and corrosion resistance, is a top choice for robust crash bar solutions. Meanwhile, 4130 steel offers a balanced approach with a tensile strength of 97,000 psi, combining strength and weight efficiency. Low Rate Locksmith also explores aluminum crash bars as a lightweight alternative, though this requires careful consideration of grades and fabrication techniques to ensure they match the strength of steel counterparts.
Proper welding techniques are paramount. Incorrect methods can lead to brittleness in aluminum or distortion in stainless steel components, compromising the integrity of the crash bars.
To help you understand their approach, consider the following:
- High-Tensile Materials: Guarantees rigidity but necessitates careful design to avoid stress transfer to the motorcycle's frame.
- Material Selection: Balances cost and durability, considering crash bar material cost.
- Engineering Precision: Utilizes advanced welding techniques to maintain material integrity.
Low Rate Locksmith's commitment to quality materials guarantees that you get durable crash bar solutions designed for longevity and safety.
Frequently Asked Questions
What Are Crash Bars Made Of?
You'll find crash bars made from stainless steel, aluminum, carbon steel, and 4130 steel. Stainless steel, particularly grades 304 and 316, provides excellent tensile strength and durability. Aluminum is lightweight but can match steel's strength if engineered well. Carbon steel is affordable and easy to work with but heavier. 4130 steel offers a strong balance of strength and weight, making it ideal for robust applications.
Are Crash Bars Any Good?
Absolutely, crash bars are lifesavers! They absorb and distribute impact energy like nobody's business, drastically reducing injury risks during accidents. Made from materials like stainless steel, they're incredibly reliable, protecting your bike's engine, frame, and fuel tank. Users rave about their effectiveness, noting minimal damage in low-speed crashes. Plus, their lightweight aluminum variants enhance handling without compromising protection. High-quality crash bars are low-maintenance and withstand harsh environments, making them a smart investment.
What Is the Difference Between a Panic Bar and a Crash Bar?
The difference between a panic bar and a crash bar lies in their function and application. You'll find panic bars on commercial doors to guarantee rapid, keyless egress during emergencies. Conversely, crash bars are mounted on motorcycles to protect the engine, frame, and rider's legs during accidents. Panic bars focus on building safety and accessibility, while crash bars aim to minimize damage and enhance rider safety in collisions.
Do Crash Bars Protect Your Legs?
Absolutely, crash bars can offer a comforting layer of protection for your legs during a mishap. They act like shields, absorbing and distributing impact forces, which reduces direct contact between the motorcycle's frame and your legs. However, it's essential to choose high-quality materials like stainless steel for maximum strength. While they can mitigate injuries in many situations, be aware that high-speed scenarios might still pose risks. Always verify compatibility with your bike.
Conclusion
In your quest for the most durable crash bars, you've navigated through a labyrinth of materials—stainless steel, aluminum, and plastic-covered options. Each boasts unique strengths like a knight's armor. Corrosion resistance and impact resilience stand as sentinels of quality. Rigorous testing guarantees these barriers are battle-ready. By comparing these materials, you witness a symphony of engineering prowess. Low Rate Locksmith's unwavering commitment to top-tier materials guarantees your vehicle's protection is nothing short of bulletproof.